机床再制造产品受到用户普遍认可
2008-10-20 15:36:23
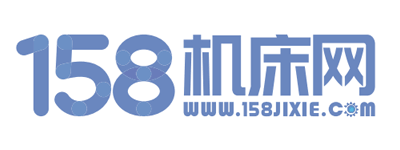
随着企业改革的加快,近年来国内机床企业更加注重突出主业,改变过去大而全、小而全的模式,所以很多企业改制后把为企业主业服务的机修车间、分厂等副业分离出去。如北京的一机床、二机床、北人、北重等企业,都把这块分离了出来。
同时,一批科研院所大专院校的技术人员、国企分流人员组合的非国企维改公司也应运而生,形成了新兴的机床维修改造行业。
三类再制造模式
从目前我国机床再制造的现有模式分析,主要有三大类:再制造商与用户之间的订单式服务模式、回收二手旧机床进行再制造模式及机床置换模式。
其中,再制造商为用户提供的订单式服务是目前我国机床再制造的主要模式。大多是再制造商通过投标等方式为用户提供老旧机床设备的再制造升级。根据用户的要求,签订合同和技术协议,再制造之后,按照技术协议进行验收。
当前,一些大重型机床的改造主要采取再制造公司的技术人员走出去,依靠用户的场地及设备,进行现场维改的方式。不同的公司技术特长不同,其薄弱环节采取分包的方式进行。
例如,机强电弱的企业,通常把电部分包给其他公司,反之亦然。加工能力薄弱公司的就把加工外协。又如国外系统的备品配件,公司间都有相互的技术协议支持。但经营方式都是采取机电结合、技术互补、统一承包的方式。
目前,一些比较大的再制造商可以为客户提供机电液一站式交钥匙服务。一般大型机床、重型机床都是单件的再制造,很难形成批量。因为很多重型机床吨位很大,价值很高,一台价值上千万元甚至几千万元。
与此同时,回收二手旧机床进行再制造也是通用的一种模式。目前,国内少数公司在尝试回收废旧机床,通过整机再制造升级后再进行销售的做法。这也是我们理解的真正意义上的机床再制造,如北京凯奇就对一批进口旧机床采取了这种做法。目前这种情况还是非常少。主要是买进旧机床需要占用大量资金、场地等,而专业维改企业在这些方面往往都很薄弱。
此外,一些原始机床制造商也在尝试机床置换的模式,也就是回收已售出的旧机床进行再制造,为用户提供以旧换新服务。
再制造的三大主体
目前,在中国从事机床再制造的主要力量是专业机床再制造企业,习惯称为机床维修改造企业,此外还有机床制造企业及数控系统制造企业,这三类企业构成了当前国内机床再制造的主体。
在我国,专业维改企业大大小小约有几百家。其中,北京圣蓝拓、北京凯奇、武汉赛特曼、武汉华中自控、唐山重型机床等5家企业,再制造业务占同类企业总业务的40%~90%。
机床制造企业从事再制造业务有很大优势,但现实的情况是,由于新机床的市场形势非常好,这些企业往往没有精力从事再制造业务。
在我国机床制造企业中,多数没有再制造业务,其他涉及再制造的企业,其再制造业务占企业总业务的比例非常小。
另外,数控系统制造企业也有再制造业务,尤其是企业成立初期所占的业务比例较大,他们从事再制造的目的主要有两个,一是通过机床再制造推广其数控系统,取得用户的信任,树立品牌;二是在再制造的实践中锻炼自己的技术队伍,培养复合型人才。目前,这些企业的主要精力是推广他们的数控系统,再制造业务已经微乎其微了。
再制造产品受到用户单位普遍认可
目前,国内已有一些单位大量使用了再制造机床产品,如济南柴油机厂、武汉长江动力集团、重庆秋田齿轮厂、唐山中材重型机械有限公司等。
据了解,重庆秋田齿轮的100多台旧机床由重庆二机床进行了数控化再制造,每台机床的再制造费用只有同类新机床的二分之一,秋田齿轮对再制造机床非常满意。
唐山中材重型机械有限公司80%的设备都是经过再制造的进口二手设备,是典型的使用再制造产品的用户。他们表示,再制造以后的产品精度等都能达到使用要求,且再制造后的价格大约只相当于新产品价格的五分之一。
据了解,容易接受再制造机床的用户一般对机床比较了解,具有一定的使用经验和相应的机床专业知识。他们通过对新品和再制造产品的使用对比,认为购买使用再制造产品更有优势。
这些用户企业使用再制造产品的原因主要有以下三个:
一是制造周期短,尤其是大型、重型设备,如果用新产品,制造周期至少需要18个月,而二手机床再制造的周期只要8~10个月,大大节省了时间,保证了工期。对于制造企业来说,工期是非常重要的,往往节省下来的时间就可以把成本收回了。
二是价格低,再制造机床的费用大约只相当于同类新产品价格的二分之一到三分之一,一些大型重型机床甚至只相当于五分之一。
三是了解机床性能,认识到旧机床的稳定性比新机床更好。