关注刀具培训,提高技术水平
2008-03-14 16:19:34
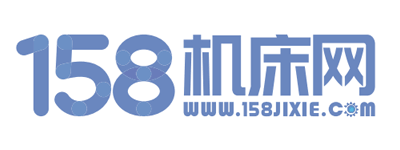
一些企业因害怕设备损坏、夹具损坏或其它原因,不敢让学习了新的加工理念、加工方法的员工应用这些方法,以至企业效益长期原地踏步,经济效益无法提高。
在现代企业中,管理者越来越重视技术培训正在成为一种普遍现象。但是据了解,80%以上的企业培训经理表示,“钱花了,培训效果却不明显”、“时间花了,培训需求还是确定不了”。这成为众多人力资源经理、企业培训师共同苦恼的问题。
在现代金属切削加工中,许多企业把技术培训的重点放在了诸如数控技术这样的新技术上,花了大量的人力、物力和财力来提高员工在数控技术方面的水平。包括一些高职院校、技师学院等,也在数控技术上作了很大的投入。但就结果而言,大量使用数控设备所换来的效果却并不十分理想。
我认为,在实际生产中数控加工能不能达到一个理想的效果,有赖于多方面的共同作用,如数控设备、数控技术、机床技术、刀具技术、工艺编制等等。这就像一个由多块木板箍成的水桶,最多能盛多少水,并不取决于那块最高的木板,而是取决于那块最低的木板。只要我们在众多的相关技术上有一项不能过关,我们使用数控机床的效果就将是有限的。
现在有关机械加工尤其是数控加工的普通高等教育和高等职业教育中,过分强调数控技术的重要性,大量削减了有关夹具、刀具、工艺、测量等等的基础技术的内容,以至于毕业的学员有点像跛了脚,怎么也走不好路。
就拿我比较熟悉的刀具技术来说,我非常赞同西北工业大学何琼儒教授的这一论述:没有切削加工和刀具技术的进步,要发展现代机械制造技术是没有保证的。
正如前面所述,在现在的普通高等教育和高等职业教育中,包括刀具教育在内的机械基础教育已经成为机械技术和技能教育的一块“短板”。这一教育的落后,将直接影响无数机械加工企业竞争能力的提高。我们许多企业投入巨资购买大量数控设备,却用陈旧的工艺观念,低效率地使用着与数控设备极不相称的传统刀具进行加工,效率和效益的低下很难避免。打个比方,这就像在著名的奔驰或宝马或劳斯莱斯汽车上,安装了自行车的轮胎,这些名车可以发挥的能力就可想而知了。
要提高我们的数控加工水平,首先要做的是更新加工工艺理念。例如,我和一些同行讲过很多次,加工的效益通常不是靠节省刀具费用而得到的。德国某大学的统计,在他们那里的汽车零部件制造企业中,刀具费用大约占制造成本的4%,而原中国刀协常务理事赵炳桢先生则告诉我,中国企业的刀具消耗大约只有3%左右。我们可以想一下,即使数控机床使用者能够得到完全免费的刀具,他们最多也不过可以节约3%~4%的成本——而实际上刀具长期的完全免费是不可能的。而如果效率提高20%的话,大约可以节约15%的成本。这一结果应该是诱人的。我认为我们每一家企业应该去争取这样的结果,至少应该为争取这一结果作好准备。
如何才能争取到这样的结果呢?
在技术上,我们应该关注适应我们加工需要的刀具技术的新进展,关注刀具新的应用方法。而获得这些信息的途径、可以是平面媒体、网络媒体、培训班、研讨会、展览会,也可以是刀具企业业务人员来访的时候。这些途径各有优势,而培训无疑是其中一个很有效的途径。
当然,想通过参加培训来提高自己的技术素养,首先应该了解自己的培训需求,了解准备参加的培训班能多大程度上满足自己的培训需求。
就参加者而言,要想在一个培训班完全满足自己的需求又没有冗余,几乎是不现实的。我们首先要明确自己首要的需求,力求能够挑选参加符合自己首要需求的培训。例如,关于我们今年计划要举办的首届刀具设计制造培训,是希望能帮助一些刀具制造企业搞清在整体刀具尤其是整体钻孔刀具方面的全局性思路,让刀具制造企业能迅速地发现自己的那块“短板”,提高这些企业造刀的整体水平。
因为我们认为,发现和改造“短板”,比改良“长板”能更快、更有效。至于期望在某一个更细节的专业方面得到培训的,也许这个班就不是他们的最佳选择了。
其次,我们应该认识到,培训绩效是个积累的过程。由于时间、费用和基础水平的限制,希望通过一两次培训就得到质的飞跃,是不符合实际的想法。我们应该设法通过一次培训,使我们在一两个环节上得到提升,使那块“短板”在通过改进之后不再成为“短板”。联想董事会主席柳传志曾经有一个形象的比喻:“企业发展就如同夯土一样,撒一层土夯实了,再撒一层土再夯实。”我们技术水平的提高也是这样。我们应该也必须树立终身接受教育、终身接受培训的理念。
作为企业,我们应该为接受培训回到工作岗位的员工创造应用培训成果的条件。提高加工效率是需要用实践来证明的。长此以往,企业的竞争能力将受到很大的伤害。我们应该在培训后一段时间内鼓励员工应用