加强产学研结合提高大型铸件自主创新能力
2008-06-10 15:46:28
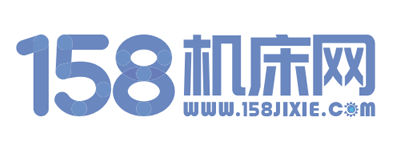
中国已是制造大国,但远不是制造强国。中国装备制造业的突出问题是自主创新能力不强,制造技术基础薄弱。大型铸锻件的质量及国产化问题十分严峻。2006年初,曾培炎副总理专门批示:重大装备国产化项目中,大型关键铸锻件,依靠进口供货,国产件能力、质量难以满足要求,已成为重大装备制造业发展的瓶颈,并受制于人。
经过一年多来的努力奋斗,特大型铸件科技攻关,特别是三峡水轮机叶轮大型铸件提高自主创新能力等方面已取得突破和进展。
市场牵引、企业主体
市场需求是推动装备制造业发展和自主创新能力提高的根本动力,要充分发挥市场牵引作用。
三峡水轮发电机组单机容量为700MW,总装机32台,其中左岸机组14台、右岸机组12台、地下机组6台。右岸机组分别由哈尔滨电机厂有限责任公司(简称哈电)、东方电机股份有限公司(简称东电)、阿尔斯通分别制造4台。地下机组6台,由右岸三家制造商分别制造2台。现左岸14台机组已全部发电,右岸12台机组已发电3台,其余机组正在制造中,哈电、东电已成长为左岸的国际招标的优胜者。但是,作为水轮机的核心转轮组成部分特大型铸件上冠、下环、叶片无论是左岸还是右岸机组几乎全部依赖进口。据预测,中国在建成32台,三峡水轮发电机组后,还将新建150台700MW以上的大型水轮发电机组。
随着中国经济的高速增长和国际经济的复苏,国际市场上大型铸锻件资源日渐紧缺,价格飞涨,交货远远不能满足主机厂的要求。为了加快大型铸件国产化,突破重型装备制造业的瓶颈,避免受制于人,国内特大型铸件主要制造厂商纷纷开始加快研制的步伐。因此,除原来第一重型集团公司(一重)、第二重型集团公司(二重)等研制单位外,哈电、鞍钢重型机械集团公司(鞍重)、大连重工重型机械集团公司(大重)及银川共享铸钢公司(共享)在三峡总公司的支持下,自告奋勇,自筹经费,增添装备,主动承担起三峡水轮发电机等特大型铸件的研制任务。
鞍重在三峡总公司的支持下,没有伸手要条件,自己承担浇铸数百吨重的特大型水轮机铸件的风险。鞍重先在试制彭水电站水轮机上冠、下环铸件成功,取得经验后,又请专家对三峡水轮机叶轮下环铸件铸造工艺方案进行评审。终于试制成功三峡水轮机叶轮下环铸件,并于2007年3月通过鉴定。
哈电承制的三峡左岸23号机转轮叶片由罗马尼亚和斯洛文尼亚进口,其中斯洛文尼亚的后三片叶片严重脱期达八个月,哈电23号机2008年发电目标面临难以实现的困境。因此,哈电紧急制造三件三峡叶片,研制目标及制造技术水平均超过罗马尼亚和斯洛文尼亚制造的叶片。哈电经过十几炉精炼钢水的摸索,完全掌握了超纯净钢水的冶炼技术。铸造工艺方法利用哈电已获得巨型叶片铸造工艺专利方法进行研制。哈电制造的三件三峡叶片于2007年8月通过鉴定(图2),成为继二重、一重后,第三个成功制造三峡叶片的企业。
大连重工重型机械集团公司及银川共享铸钢公司等在三峡总公司的支持下也已开始试制三峡上冠及叶片铸件。共享铸钢公司试制成功的叶片达到国际先进水平,并于2007年12月通过鉴定(图3)。
以上实例充分地说明:企业是技术创新的主体,也是提高装备制造业自主创新能力的需求主体、投资主体和实施主体。
更值得一提的是,2007年12月,三峡右岸工程的一个叶轮在焊接组装过程中有一件从斯洛文尼亚进口的叶片出现了质量事故,严重影响工程进度。哈电紧急采用了刚刚试制成功的叶片进行更换,才确保了工程进度。事故原因现已查明是进口叶片的机械性能没有达到三峡叶片的技术要求。从以上正、反两方面的实例,更进一步说明:一定要立足自主创新,绝不能盲目依赖国外。
高校及院所在技术创新中大有可为
重大装备的设计与制造技术难度很大、涉及多个学科领域,单靠一个企业自身的力量往往是不够的,应该在政府的引导、推动下,实现产、学、研之间的紧密联合,或进一步结成联盟,共同对重大装备的共性技术、关键技术进行攻关,实现双赢或多赢。
我们的体会:一是科研要面向国家目标,二是科研要有奉献精神,三是要为企业提供科学技术支撑。
科研要面向国家目标
高等工科院校要将《国家中长期科技发展纲要》中的国家目标,作为科研主攻方向,克服轻视生产实践,片面重视论文的倾向。
清华大学机械工程系一直以国家目标为科研主攻方向,早在2001年,就协助二重采用先进的计算机模拟技术,优化铸造工艺,试制成功中国第一件三峡水轮机叶轮叶片,2004年,又以“交钥匙工程”方式,从铸造工艺及模拟仿真两方面,协助马钢重机在十个月内,浇铸成功18片重200余吨的大型轧钢机机架铸件。项目合作期间,机械工程系多名教授、副教授带领研究生先后多次深入现场。该项目的完成使得“马钢双板轧机工程”提前6个月投产,为马钢公司节省外汇资金约1千万余元。
科研要有奉献精神
科学研究是要有奉献精神的。中国科学院金属研究所李依依院士领导的课题组和笔者领导的课题组以及沈阳铸造研究所等单位的专家在一年多的时间